一、认识疲劳
疲劳是材料(金属)承受循环应力或应变作用时,结构性能下降,并最终导致破坏的现象。疲劳失效是最常见的失效形式之一。文献中提供的数据显示,各种机械中,疲劳失效的零件占失效零件的60——70%。疲劳断裂失效原则上属于低应力脆断失效,疲劳中难以观察到明显的塑性变形,因为这是以局部塑性变形为主,且主要发生在结构的固有缺陷上。虽然频率对疲劳失效有一定影响,但多数情况下疲劳失效主要与循环次数有关。
01 按引起疲劳失效的应力特点可以分为:
由机械应力引起的机械疲劳和热应力(交变热应力)引起的热疲劳;
02 从循环周次可分为:
高周、低周、超高周疲劳;
03 根据载荷性质可分为:
拉-压疲劳、扭转疲劳以及弯曲疲劳等;
04 根据工件的工作环境可分为:
腐蚀疲劳、低温疲劳、高温疲劳。
一般把材料与结构发生疲劳损伤前的强度定义为“疲劳极限”。
01
冲击疲劳
是指重复冲击载荷所引起的疲劳。当冲击次数N小于500——1000次即破坏时,零件的断裂形式与一次冲击相同;当冲击次数大于105次时的破坏,零件断裂属于疲劳断裂,并具有典型的疲劳断口特征。在设计计算中,当冲击次数大于100次时,用类似于疲劳的方法计算强度。
02
接触疲劳
零件在循环接触应力作用下产生局部永久性累计损伤,经过一定循环次数后,接触表面发生麻点、浅层或深层剥落的过程,称为接触疲劳。接触疲劳是齿轮、滚动轴承和凸轮轴的典型失效形式。
03
热疲劳
由于温度循环产生循环热应力所导致的材料或零件的疲劳称为热疲劳。温度循环变化导致材料体积循环变化,当材料的自由膨胀或收缩受到约束时,产生循环热应力或循环热应变。
产生热应力情况主要有两种:
1、零件的热胀冷缩受到固持零件的外加约束而产生热应力;
2、虽然没有外加约束,但两件各部分的温度不一致,存在着温度梯度,导致各部分热胀冷缩不一致而产生热应力。
温度交变作用,除了产生热应力外,还会导致材料内部组织变化,使强度和塑性降低。热疲劳条件下的温度分布不是均匀的,在温度梯度大的地方,塑性变形严重,热应变集中较大;当热应变超过弹性极限时,热应力与热应变就不呈线性关系,此时求解热应力就要按弹塑性关系处理。热疲劳裂纹从表面开始向内部扩展,方向与表面垂直。
热应力的大小与热胀系数成正比,热胀系数越大,热应力越大。所以在选材时要考虑材料的匹配,即不同材料热膨胀系数的差别不能太大。在相同的热应变条件下,材料的弹性模量越大,热应力就越大;温度循环变化越大,即上下限温差越大,则热应力就越大;材料的热导率越低,则快速加速或冷却过程中,温度梯度越陡,热应力也越大。
04
腐蚀疲劳
腐蚀介质和循环应力(应变)的复合作用所导致的疲劳称为腐蚀疲劳。腐蚀介质与静应力共同作用产生的腐蚀破坏称为应力腐蚀。两者的区别在于,应力腐蚀只有在特定的腐蚀环境中才发生,而腐蚀疲劳在任何腐蚀环境及循环应力复合作用下,都会发生腐蚀疲劳断裂。应力腐蚀开裂,有一个临界应力强度因子KISCC,当应力强度因子KI≤KISCC,就不会发生应力腐蚀开裂;而腐蚀疲劳不存在临界应力强度因子,只要在腐蚀环境中有循环应力继续作用,断裂总是会发生的。
腐蚀疲劳与空气中的疲劳区别在于,腐蚀疲劳过程中,除不锈钢和渗氮钢以外,机械零部件表面均变色。腐蚀疲劳形成的裂纹数目较多,即呈多裂纹。腐蚀疲劳的S-N曲线没有水平部分,因此,对于腐蚀疲劳极限,一定要指出是某一寿命下的值,即只存在条件腐蚀疲劳极限。影响腐蚀疲劳强度的因素要比空气中疲劳多而且复杂,如在空气中,疲劳试验频率小于1000HZ时,频率基本上对疲劳极限没有影响,但腐蚀疲劳在频率的整个范围内都有影响。
二、疲劳寿命
当一个材料或机械部件失效时,总寿命通常由三部分组成:
裂纹萌生寿命,大量工程实践表明,实际服役过程中机械部件裂纹的萌生寿命占据疲劳寿命的绝大部分(甚至达到总寿命的90%)。
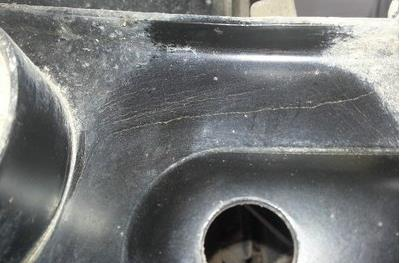
裂纹稳定扩展寿命,多数情况下,当一条微裂纹的深度达到该尺寸(约为0.1mm)时,它就沿着材料或者部件的截面稳定扩展。
失稳扩展至断裂寿命。
三、金属材料的疲劳形式
金属材料的疲劳主要有以下几种:
一般的塑性变形;
低周疲劳下的塑性变形;
高周疲劳下的塑性变形;
超高周疲劳下晶立尺寸的微观塑性变形。
四、影响材料与结构疲劳强度的因素
01 平均应力
随着平均应力(统计应力)的增加,材料的动态抗疲劳应力降低。对于同一属性的力,平均应力σm越大,则给定寿命的应力幅σa就越小。
02 应力集中
由于工作条件或加工工艺的要求,零件常带有台阶、小孔、键槽等,使截面发生突然变化,从而引起局部的应力集中,这将显著地降低材料的疲劳极限,但实验表明,疲劳极限降低的程度并不是与应力集中系数成正比。但如果要准确地预测机械部件的疲劳行为,就必须估计高应力区或者含制造缺陷的裂纹萌生寿命。
03 残余应力
文献研究指出,探讨残余应力对金属疲劳强度的影响,需在高周疲劳下才有意义,因为低周疲劳的高应变幅下残余应力将大幅度地松弛,所以在低周疲劳下显示不出多大的作用。表层残余压应力对于承受轴向载荷且疲劳裂纹起源于表面的零部件是有益的,但要注意核心部区域的残余拉应力叠加外载后发生屈服所引起的残余应力松弛问题。残余应力对零件缺口疲劳强度的作用十分显著,这是由于残余应力也存在应力集中现象和残余应力对疲劳裂纹扩展的影响更大的缘故。但残余应力的应力集中不仅与缺口几何因素有关,还与材料特性有关。
04 尺寸效应
材料的疲劳极限σ-1值通常是用小试样测定的,试样直径一般在7——12mm,而实际构件的截面往往大于该尺寸。试验指出,随着试样直径的加大,疲劳极限下降。其中,强度高的钢比强度低的钢下降的快。
05 构件表面状态
构件表面是疲劳裂纹核心易于产生的地方,而承受交变弯曲或交变扭转负荷的构件,表面应力最大。构件表面的粗糙度、机械加工的刀痕都会影响疲劳强度。表面损伤(刀痕、磨痕等)本身就是表面缺口,会产生应力集中。使其疲劳极限降低,且材料强度越高,缺口敏感性越显著,加工表面质量对疲劳极限的影响就越大。
06 环境因素
金属材料的疲劳性能还受到周围液相或气相等环境的影响。腐蚀疲劳是指金属材料在腐蚀介质和循环载荷交互作用下的响应,它通常多用于描述水相环境下材料的疲劳行为。腐蚀疲劳、低温疲劳、高温疲劳,不同气压环境、湿度环境等都是材料与环境因素共同作用下的疲劳现象。
在大气环境下,同一材料的破坏循环周次也远低于真空环境。真空环境中的裂纹萌生寿命远大于大气环境。当工件工作环境压力接近Pcr(寿命拐点处的气压定义为临界气压)时,材料的疲劳寿命就变得异常敏感。大气环境中材料的疲劳寿命(一般低于真空环境)会随着温度的升高而降低,加速裂纹扩展。环境湿度对高强度铬钢的耐久性影响较大。水汽(尤其是室温环境)对多数金属及合金的抗断裂性能有不利影响,这种不利影响取决于应力水平、载荷比、幅值等加载条件。微观组织与环境之间具有强烈的相互作用,气相环境显著影响着断口的形貌和位错滑移机制,环境与裂纹闭合之间存在着交互作用,尤其在近门槛区。环境影响程度取决于裂纹面的形貌,尤其是在深度方向上。
在低温下,金属的强度提高而塑性则降低。因此,在低温下光滑试样的高周疲劳强度比室温下有所提高,而低周疲劳强度比室温下低。对于有缺口的试样,韧性和塑性降低得更多。缺口和裂纹对低温较为敏感,即断裂时的临界疲劳裂纹长度在低温下会急剧减小。
广义的高温疲劳是指高于常温的疲劳现象。但通常情况下,由于有些零件的工作温度虽然高于室温,但并不太高。只有当温度高于0.5Tm(Tm为以热力学温度表示的熔点),或在再结晶温度以上时,出现了蠕变与机械疲劳复合的疲劳现象,这时才称为高温疲劳。
07 载荷类型
不同载荷下疲劳极限的大小顺序为:旋转弯曲<平面弯曲<压缩载荷<扭转载荷。在腐蚀介质中,加载频率的裂纹扩展的作用比较明显。在室温和试验环境下中,常规频率 (0.1——100HZ) 对钢和黄铜的裂纹扩展几乎没有任何影响。在试验中一般而言,如果试验加载频率低于250HZ,频率对金属材料的疲劳寿命的影响就较小。
08 材料缺陷
裂纹多萌生于表面,如在焊缝(孔眼)、铸钢(疏松)或次表面上(夹杂改变了局部应变场),而很少在内部萌生。裂纹萌生还取决于夹杂的数量、尺寸、性质和分布,同时也与外力的加载方向有关。此外,夹杂与基体的结合强度也不容忽视。显微裂纹是百万周次寿命材料中最危险的缺陷,显微曲线则是控制着10亿周次寿命材料的寿命。由于微观尺寸下材料内部存在缺陷的几率远大于材料表面,因此超高周疲劳加载时内部萌生裂纹的几率自然大于表面。
脆性材料不存在应力降低或加工硬化现象,一旦出现缺口,在较小的名义应力条件下就可能发生断裂。经验表明,当存在缺口时,金属的疲劳极限降低,并且塑性越差,缺口对疲劳极限的影响越大。
09 加工方式
文献中指出,在疲劳试验试样的制备过程应是导致试验数据离散性最重要的环节,如车、铣和校直等机械加工方式都与试样的最终制备质量有关。正是由于制备方式和热处理因素会影响材料的疲劳性能,尤其是热处理的影响较大,因而即使是同一批次和尺寸、形貌完全相同的试验也很难完全重复以前的疲劳试验结果。由此可见,工件的生产加工因素会导致零部件的实际疲劳寿命偏离分析计算的期望寿命值。
10 材料属性
高周疲劳强度(N>106时)与材料的硬度有关,而对于中低周疲劳,韧性是一种重要指标。在高应力条件下,高强度钢由于韧性较差,其疲劳性能较低,而低应力情况下,则具有较好的抗疲劳性能。低强度钢与之相反,中强度钢居中。一般说来弹性模量越高,裂纹扩展速率越低。晶粒尺寸的影响对裂纹扩展的影响仅存在于两种极端扩展的情况:△K→△Kth和△Kmax→△KC,对中速裂纹扩展特性没有明显的影响。断裂韧性KIC(或KC)与扩展速率是相互联系的。一般认为,材料韧性的增加会降低裂纹的扩展速度。
五、疲劳试验数据的离散性
试验设备和试样本身是造成疲劳试验数据(或结果)离散性的根本原因。据文献分析介绍,在测定零构件的疲劳寿命时,名义载荷相对实际载荷有3%的误差,就会使疲劳寿命产生60%的误差,极端情况可能会导致120%的寿命误差。而对于疲劳试验机来说,3%误差是完全允许的。不过文中也提到,在静力破坏试验中,即使对强度分散性较大的铸造材料和玻璃等,也不像疲劳寿命那样存在严重的分散性。
疲劳试验结果的离散性与材料属性有关,具体有:材料内部的固有特性;试验的制备过程,试验的外部环境。其中,试验制备过程是导致数据离散性最重要的环节,尤其是热处理。材料内的夹杂和第二相颗粒等是造成试验数据离散的本质原因,目前其作用机制仍不十分清楚。
六、结构疲劳设计方法的发展
安全寿命法
设计应力低于疲劳极限,认为结构中无缺陷。
失效安全法
设计应力与平面缺陷情况下的剩余强度有关,该设计方法允许存在可接受的缺陷
安全裂纹法
允许存在确定性可预测的扩展裂纹。
局部失效法
能够解决金属疲劳分析中的一些问题,目前在法国广泛应用。20世纪90年代超高周疲劳试验技术的兴起,充分说明一些微观缺陷(如夹渣、气孔、锻造形成的大尺寸晶粒等)对材料的疲劳寿命也具有重要的影响。
对于钢材料,在缺少材料的疲劳试验数据时,可由材料的拉伸强度极限做出近似的S-N曲线。把疲劳极限与拉伸强度和试样断裂伸长率联系起来是具有较高精度的一种估算方法。
在材料与结构的疲劳分析中,要优先从试验中得到结论而不是盲目地相信弹塑性计算,唯有如此,才能确保数据的可靠性。
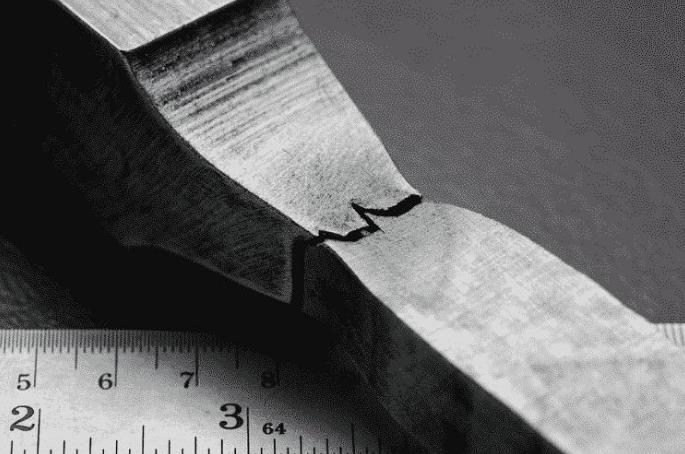
七、疲劳试验常见术语汇总
1
循环屈服强度
Cyclic yield strength
符号:σy
循环应力应变曲线0.2%应变偏离处的屈服强度。
2
弹性应变
Elastic strain
符号:εe
总应变的弹性部分,εe=εt-εp。
3
疲劳极限
Fatigue limit
应力振幅的极限值,在这个值以下,被测试样能承受无限次的应力周期变化。
注:见N个循环后的疲劳强度。
4
疲劳缺口系数
Fatigue notch factor
符号:Kf
在相同的疲劳寿命下,缺口试样的疲劳强度同平面试样疲劳强度的比值。
5
疲劳裂纹扩展速率
Fatigue crack growth rate
符号:da/dN
每个循环周期内裂纹扩展的长度(mm/周)。
6
疲劳裂纹扩展的门槛值
Fatigue crack growth threshold
符号:ΔKth
da/dN 趋近于0 的时候,ΔK 的渐近线的值。
注 :对多数材料门槛值定在8-10mm/周对应的应力强度因子范围。
7
疲劳延性系数
Fatigue ductility coefficient
符号:εf’
log(εα)-log(2Nf) 曲线上相交于2Nf=1的应变值。
8
疲劳寿命
Fatigue life
符号:Nf
达到疲劳失效判据的实际循环数。
9
振幅
amplitude
变化范围的一半。
注:常用作下脚标,如εa,应变振幅。
10
循环
Cycle
循环性重复作用的力、应力、应变等最小的时间段。
11
力比或应力比
Force ratio or stress ratio
符号:R
一个循环内力或应力的最小值同最大值的比率。
12
频率
Frequency
疲劳试验中,单位时间内应力或应变变化的循环次数。
13
高周疲劳试验
High cycle fatigue test
应力特性主导的,疲劳寿命相对较长的疲劳试验。
14
滞后回线
Hysteresis loop
一个循环中试样的闭合应力应变响应曲线。
15
循环应变硬化指数
Cyclic strain hardening exponent
符号:n'
循环曲线log(σa)-log(εpa) 的斜率。
16
循环强度系数
Cyclic strength coefficient
符号:K’
循环曲线log(σa)-log(εpa) 上相交于εpa=1的应力值。
17
疲劳强度
Fatigue strength
符号:S
在指定寿命下使试样失效的应力水平。
18
N次循环后的疲劳强度
Fatigue strength at N cycles
符号:σN
在规定的应力比下,使试样的寿命为N个循环的应力振幅值。
注:一些金属通常显现不出定义中的“疲劳极限”或“耐久极限”。这是因为,在低于此应力作用下,金属可以承受无数此循环。典型的,应力曲线中的平台被认为是传统的“疲劳极限”或“耐力极限”而得出的,但是在这个应力水平以下也会发生失效。
19
疲劳强度指数
Fatigue strength exponent
符号:b
曲线log(εe)-log(2Nf) 的斜率。
20
疲劳试验
Fatigue test
在试样上施加重复的试验力或变形、或变化的力或变形,得到疲劳寿命、给定寿命内的疲劳强度等的试验。
21
降K试验
K-decreasing test
试验中的规则化K 梯度值是负值,降K 试验的进行是在裂纹扩展期间连续降低或逐级减少应力强度因子。
22
应力比
Stress ratio
符号:Rs
疲劳试验任一循环中,最小应力与最大应力的比。Rs=σmin/σmax,也称作载荷比。
23
应力级差
Stress step
符号:d
当以逐级变化加载方法进行试验时,相邻应力水平的差值。
24
热应变
Thermal strain
符号:εth
由于温度变化产生自由膨胀时所对应的应变。
25
增K试验
K-increasing test
试验中的C 是正值,标准试样的恒幅载荷试验是增K试验,其C值是正值并在试验中增加。
26
低周疲劳试验
Low cycle fatigue test
疲劳试验进行在循环塑性特征为主的区域,并且疲劳寿命相对较短。
27
最大应力
Maximum stress
符号:σmax,Smax
在应力循环中,应力的最大代数值。
28
平均应力
Mean stress
符号:σm,Sm
最大应力与最小应力代数和的一半。
29
应力范围
Stress range
符号:Δσ,ΔS
最大应力和最小应力的算术差。
Δσ=σmax-σmin or ΔS=Smax-Smin
30
热机械疲劳试验
Thermomechanical fatigue test
符号:TMF
试验部分的理论平均温度和张力场,同时由外部循环施加条件下的疲劳试验。
31
总应变
Total strain
符号:εt εtot
标距内的长度变化除以原始标距长度。
32
机械应变
Mechanical strain
符号:εm
与试样上施加的力有关而与温度无关的应变。
33
最小应力
Minimum stress
符号:σmin,Smin
在应力循环中,应力的最小代数值。
34
规则化K梯度
Normalized K-gradient
符号:C
K 随裂纹增加而变化的分式比率
[mm-1]C=1/K(dK/da)=1/Kmax(dKmax/da)=1/Kmin(dKmin/da)=1/ΔK(dΔK/da)
35
塑性应变
plastic strain
符号:εp
在受控应变中的塑性应变部分。
36
S-N曲线
S-N curve
应力寿命曲线。
37
应变幅
Strain amplitude
符号:εa
在一个应变循环中,最大应变和最小应变代数差的一半。
38
应变比
Strain ratio
符号:Rε
疲劳过程中任一循环最小与最大应变的比值。
Rε=εmin/εmax
39
应力幅
Stress amplitude
符号:σa,Sa
在应力循环中,最大应力和最小应力之间代数差的一半。
40
应力水平
Stress level
符号:S
试验期间加在试样上的间接控制变量。
注:事实上力是直接控制变量。
文章转摘来源:贤集网